HPGR (Morrell-Tondo-Shi): Difference between revisions
md>Scott.Munro m (→Example) |
imported>Scott.Munro |
||
(3 intermediate revisions by 2 users not shown) | |||
Line 1: | Line 1: | ||
== Description == | == Description == | ||
This article describes the Morrell | This article describes the Morrell-Tondo-Shi (Morrell et al., 1997) model for comminution by High Pressure Grinding Rolls (HPGR), verified for simulation and scale-up by Daniel and Morrell (2004).{{Morrell et al. (1997)}}{{Daniel and Morrell (2004)}} | ||
== Model theory == | == Model theory == | ||
Line 7: | Line 7: | ||
[[File:HPGRMorrellTondoShi5.png|thumb|450px|Figure 1. Schematic diagram showing the Whiten crusher sub-model arrangement of the Morrell-Shi-Tondo approach (after Morrell et al., 1997).{{Morrell et al. (1997)}}]] | [[File:HPGRMorrellTondoShi5.png|thumb|450px|Figure 1. Schematic diagram showing the Whiten crusher sub-model arrangement of the Morrell-Shi-Tondo approach (after Morrell et al., 1997).{{Morrell et al. (1997)}}]] | ||
{{ | The Morrell-Tondo-Shi (Morrell et al., 1997) model simulates HPGR size reduction by linking three separate instances of the [[Crusher (Whiten)|Whiten crusher]] model.{{Morrell et al. (1997)}} The crusher instances represent comminution by the sub-processes of ''pre-crushing'', ''edge crushing'', and ''compressed bed'' crushing, as illustrated in Figure 1. | ||
=== Pre, edge and bed crushers === | |||
:''Main article'': See [[Crusher (Whiten)]] for a full description of the Whiten crusher model. | |||
Behaviour of the pre-crusher process is determined by the ''critical gap'', <math>x_{\rm c}</math> (mm), which is defined as the largest particle in the feed which will be nipped and comminuted in the HPGR machine. The critical gap can be estimated by the relation: | |||
:<math>x_{\rm c} = 0.5 \left[ (D + x_{\rm g}) - \left ( \dfrac{4 \rho_{\rm g} D x_{\rm g}}{\rho_{\rm c}} \right )^{0.5} \right ]</math> | |||
where: | |||
* <math>D</math> is the diameter of the rolls (m) | |||
* <math>x_{\rm g}</math> is the working gap (m) | |||
* <math>\rho_{\rm g}</math> is the bulk density of the discharge cake solids (t/m<sup>3</sup>) | |||
* <math>\rho_{\rm c}</math> is the bulk density of the feed solids (t/m<sup>3</sup>) | |||
The pre, edge and bed Whiten crusher parameter values in Table 1 are recommended by Morrell et al. (1997): | |||
:{| class="wikitable" | |||
|+ Whiten crusher parameter values for the Morrell-Tondo-Shi HPGR model (after Morrell et al., 1997).{{Morrell et al. (1997)}} | |||
|- | |||
! Pre-crusher !! Edge crusher !! Bed crusher | |||
|- style="vertical-align:top;" | |||
| | |||
<math> | |||
\begin{array}{l} | |||
(K_1)_{\rm Pre} = (c_{K_1})_{\rm Pre} (K_2)_{\rm Pre}\\ | |||
(c_{K_1})_{\rm Pre}=0.64 \text{ or user-defined value}\\ | |||
(K_2)_{\rm Pre} = x_{\rm c}\\ | |||
(K_3)_{\rm Pre} = 1.0 \text{ or user-defined value}\\ | |||
(t_{10})_{\rm Pre} = 12.04 \text{ or user-defined value}\\ | |||
\end{array} | |||
</math> | |||
| | |||
<math> | |||
\begin{array}{l} | |||
(K_1)_{\rm Edge} = (c_{K_1})_{\rm Edge} (K_2)_{\rm Edge}\\ | |||
(c_{K_1})_{\rm Edge}=0.64 \text{ or user-defined value}\\ | |||
(K_2)_{\rm Edge} = x_{\rm g}\\ | |||
(K_3)_{\rm Edge} = 1.0 \text{ or user-defined value}\\ | |||
(t_{10})_{\rm Edge} = 12.04 \text{ or user-defined value}\\ | |||
\end{array} | |||
</math> | |||
| | |||
<math> | |||
\begin{array}{l} | |||
(K_1)_{\rm Bed} = 0\\ | |||
(K_2)_{\rm Bed} = x_{\rm g}\\ | |||
(K_3)_{\rm Bed} = \text{User-defined value}\\ | |||
(t_{10})_{\rm Bed} = \text{User-defined value}\\ | |||
\end{array} | |||
</math> | |||
|} | |||
Particles in the pre-crusher and edge crusher zones are assumed to undergo a ''single-particle breakage'' process, much like a conventional cone crusher: | |||
* The appearance function and energy-size reduction parameters determined from drop weight tests characterise single particle breakage behaviour. | |||
Particles in the bed crusher are subject to contact forces from surrounding particles and undergo a ''compressed bed breakage'' process: | |||
* Compressed bed appearance function and energy-size reduction parameters may be determined from piston and die tests, and are notably different from the single particle breakage parameters for the same ore. | |||
* The appearance function and energy-size reduction matrices for compressed bed breakage are specified at <math>t_{10} = \{ 10, 30, 50 \}</math> intervals, rather than the <math>t_{10} = \{ 10, 20, 30 \}</math> intervals of single particle breakage, due to the additional size reduction obtained from HPGR devices. | |||
=== Edge split === | |||
The split of pre-crushed material to the edge crusher process, <math>f</math> (frac), is given by: | |||
:<math>f = \gamma \dfrac{x_{\rm g}}{L}</math> | |||
where: | |||
* <math>\gamma</math> is the edge split factor (-) | |||
* <math>L</math> is the length of the rolls (m) | |||
=== Throughput === | |||
The throughput capacity of an HPGR machine may be estimated from:{{Daniel and Morrell (2004)}} | |||
:<math>Q = 3600 \cdot U L x_{\rm g} \rho_{\rm g} c</math> | |||
where | |||
* <math>Q</math> is the HPGR throughput solids mass flow rate (t/h) | |||
* <math>U</math> is the circumferential velocity of the rolls (m/s) | |||
* <math>L</math> is the length of the rolls (m) | |||
* <math>x_{\rm g}</math> is the working gap (m) | |||
* <math>\rho_{\rm g}</math> is the discharge cake solids bulk density (t/m<sup>3</sup>) | |||
The parameter <math>c</math> is a correction factor applied to the theoretical throughput to account for material slip at the rolls face: | |||
:<math>c = \dfrac{Q_{\rm m}}{Q_{\rm c}}</math> | |||
where <math>Q_{\rm m}</math> is the measured throughput of an HPGR unit (t/h) and <math>Q_{\rm c}</math> is the theoretical throughput calculated from <math>Q = 3600 \cdot U L x_{\rm g} \rho_{\rm g}</math> (t/h). | |||
Morrell et al. (1997) suggests material slip is a function of rolls speed and the dimensionless rolls gap, and that the correction factor exhibits a linear relationship of the form <math>y = a - bx</math>, i.e.: | |||
:<math>c = c_{\rm a} - c_{\rm b} \left ( U \frac{x_{\rm g}}{D} \right ) </math> | |||
The parameters <math>c_{\rm a}</math> and <math>c_{\rm b}</math> can be determined from measurements on an operating HPGR at various throughputs, roll speeds and working gaps. | |||
=== Power === | |||
The gross power draw of the HPGR machine, <math>P_{\rm Gross}</math> (kW), is computed as: | |||
:<math>P_{\rm Gross} = P_{\rm No\text{-}load} + (k_{\rm P})_{Edge} \cdot (P_{\rm Pre} + P_{\rm Edge}) + (k_{\rm P})_{Bed} \cdot P_{\rm Bed}</math> | |||
where: | |||
* <math>P_{\rm No-load}</math> is the no-load (idling) power draw of the machine (kW) | |||
* <math>P_{\rm Pre}</math> is the power draw estimated by the pre-crusher model (kW) | |||
* <math>P_{\rm Edge}</math> is the power draw estimated by the edge crusher model (kW) | |||
* <math>P_{\rm Bed}</math> is the power draw estimated by the compressed bed crusher model (kW) | |||
* <math>(k_{\rm P})_{Edge}</math> and <math>(k_{\rm P})_{Bed}</math> are user-defined scaling factors that correct model-estimated power to observed power (kW/kW) | |||
The ''specific comminution energy'', <math>E_{\rm cs}</math> (kWh/t), of an HPGR is defined as: | |||
:<math>E_{\rm cs} = \dfrac{P_{\rm Gross}}{Q}</math> | |||
== Excel == | == Excel == | ||
Line 34: | Line 141: | ||
\rho_{\rm g}\text{ (t/m}^3\text{)}\\ | \rho_{\rm g}\text{ (t/m}^3\text{)}\\ | ||
\gamma\text{ (-)}\\ | \gamma\text{ (-)}\\ | ||
c_{\rm a}\text{ (-)}\\ | |||
c_{\rm b}\text{ (-)}\\ | |||
P_{\rm NoLoad}\text{ (kW)}\\ | P_{\rm NoLoad}\text{ (kW)}\\ | ||
(k_{\rm P})_{\rm Edge}\text{ (kW/kW)}\\ | (k_{\rm P})_{\rm Edge}\text{ (kW/kW)}\\ | ||
Line 42: | Line 149: | ||
(K_3)_{\rm Pre}\text{ (-)}\\ | (K_3)_{\rm Pre}\text{ (-)}\\ | ||
(t_{10})_{\rm Pre}\text{ (}%\text{)}\\ | (t_{10})_{\rm Pre}\text{ (}%\text{)}\\ | ||
(K_1)_{\rm Bed}\text{ (mm)}\\ | |||
(K_3)_{\rm Bed}\text{ (-)}\\ | (K_3)_{\rm Bed}\text{ (-)}\\ | ||
(c_{K_1})_{\rm Edge}\text{ (mm/mm)}\\ | (c_{K_1})_{\rm Edge}\text{ (mm/mm)}\\ | ||
Line 54: | Line 162: | ||
\end{bmatrix},\;\;\;\;\;\; | \end{bmatrix},\;\;\;\;\;\; | ||
HPGRFeed= \begin{bmatrix} | \mathit{HPGRFeed}= \begin{bmatrix} | ||
(Q_{\rm M,F})_{11}\text{ (t/h)} & \dots & (Q_{\rm M,F})_{1m}\text{ (t/h)}\\ | (Q_{\rm M,F})_{11}\text{ (t/h)} & \dots & (Q_{\rm M,F})_{1m}\text{ (t/h)}\\ | ||
\vdots & \ddots & \vdots\\ | \vdots & \ddots & \vdots\\ | ||
Line 62: | Line 170: | ||
:<math> | :<math> | ||
SP\_Appearance= \begin{bmatrix} | \mathit{SP\_Appearance}= \begin{bmatrix} | ||
\begin{bmatrix} | \begin{bmatrix} | ||
(t_{75})_{10}\text{ (}\%\text{)} & (t_{50})_{10}\text{ (}\%\text{)} & (t_{25})_{10}\text{ (}\%\text{)} & (t_{4})_{10}\text{ (}\%\text{)} & (t_{2})_{10}\text{ (}\%\text{)}\\ | (t_{75})_{10}\text{ (}\%\text{)} & (t_{50})_{10}\text{ (}\%\text{)} & (t_{25})_{10}\text{ (}\%\text{)} & (t_{4})_{10}\text{ (}\%\text{)} & (t_{2})_{10}\text{ (}\%\text{)}\\ | ||
Line 76: | Line 184: | ||
\end{bmatrix},\;\;\;\;\;\; | \end{bmatrix},\;\;\;\;\;\; | ||
SP\_Ecst10Size= \begin{bmatrix} | \mathit{SP\_Ecst10Size} = \begin{bmatrix} | ||
\begin{bmatrix} | \begin{bmatrix} | ||
(d_{\rm p})_1\text{ (mm)} & \dots & (d_{\rm p})_k\text{ (mm)} \\ | (d_{\rm p})_1\text{ (mm)} & \dots & (d_{\rm p})_k\text{ (mm)} \\ | ||
\end{bmatrix}\\ | \end{bmatrix}_{\rm SP}\\ | ||
\begin{bmatrix} | \begin{bmatrix} | ||
( | (E_{\rm cs})_{10,1}\text{ (kWh/t)} & \dots & (E_{\rm cs})_{10,k}\text{ (kWh/t)}\\ | ||
( | (E_{\rm cs})_{20,1}\text{ (kWh/t)} & \dots & (E_{\rm cs})_{20,k}\text{ (kWh/t)}\\ | ||
( | (E_{\rm cs})_{30,1}\text{ (kWh/t)} & \dots & (E_{\rm cs})_{30,k}\text{ (kWh/t)}\\ | ||
\end{bmatrix}_{\rm SP,1}\\ | \end{bmatrix}_{\rm SP,1}\\ | ||
\vdots\\ | \vdots\\ | ||
\begin{bmatrix} | \begin{bmatrix} | ||
( | (E_{\rm cs})_{10,1}\text{ (kWh/t)} & \dots & (E_{\rm cs})_{10,k}\text{ (kWh/t)}\\ | ||
( | (E_{\rm cs})_{20,1}\text{ (kWh/t)} & \dots & (E_{\rm cs})_{20,k}\text{ (kWh/t)}\\ | ||
( | (E_{\rm cs})_{30,1}\text{ (kWh/t)} & \dots & (E_{\rm cs})_{30,k}\text{ (kWh/t)}\\ | ||
\end{bmatrix}_{\rm SP,m}\\ | \end{bmatrix}_{\rm SP,m}\\ | ||
\end{bmatrix} | \end{bmatrix} | ||
Line 98: | Line 206: | ||
\begin{bmatrix} | \begin{bmatrix} | ||
(t_{75})_{10}\text{ (}\%\text{)} & (t_{50})_{10}\text{ (}\%\text{)} & (t_{25})_{10}\text{ (}\%\text{)} & (t_{4})_{10}\text{ (}\%\text{)} & (t_{2})_{10}\text{ (}\%\text{)}\\ | (t_{75})_{10}\text{ (}\%\text{)} & (t_{50})_{10}\text{ (}\%\text{)} & (t_{25})_{10}\text{ (}\%\text{)} & (t_{4})_{10}\text{ (}\%\text{)} & (t_{2})_{10}\text{ (}\%\text{)}\\ | ||
(t_{75})_{30}\text{ (}\%\text{)} & (t_{50})_{30}\text{ (}\%\text{)} & (t_{25})_{30}\text{ (}\%\text{)} & (t_{4})_{30}\text{ (}\%\text{)} & (t_{2})_{30}\text{ (}\%\text{)}\\ | (t_{75})_{30}\text{ (}\%\text{)} & (t_{50})_{30}\text{ (}\%\text{)} & (t_{25})_{30}\text{ (}\%\text{)} & (t_{4})_{30}\text{ (}\%\text{)} & (t_{2})_{30}\text{ (}\%\text{)}\\ | ||
(t_{75})_{50}\text{ (}\%\text{)} & (t_{50})_{50}\text{ (}\%\text{)} & (t_{25})_{50}\text{ (}\%\text{)} & (t_{4})_{50}\text{ (}\%\text{)} & (t_{2})_{50}\text{ (}\%\text{)}\\ | |||
\end{bmatrix}_{\rm Bed,1}\\ | \end{bmatrix}_{\rm Bed,1}\\ | ||
\vdots\\ | \vdots\\ | ||
\begin{bmatrix} | \begin{bmatrix} | ||
(t_{75})_{10}\text{ (}\%\text{)} & (t_{50})_{10}\text{ (}\%\text{)} & (t_{25})_{10}\text{ (}\%\text{)} & (t_{4})_{10}\text{ (}\%\text{)} & (t_{2})_{10}\text{ (}\%\text{)}\\ | (t_{75})_{10}\text{ (}\%\text{)} & (t_{50})_{10}\text{ (}\%\text{)} & (t_{25})_{10}\text{ (}\%\text{)} & (t_{4})_{10}\text{ (}\%\text{)} & (t_{2})_{10}\text{ (}\%\text{)}\\ | ||
(t_{75})_{30}\text{ (}\%\text{)} & (t_{50})_{30}\text{ (}\%\text{)} & (t_{25})_{30}\text{ (}\%\text{)} & (t_{4})_{30}\text{ (}\%\text{)} & (t_{2})_{30}\text{ (}\%\text{)}\\ | (t_{75})_{30}\text{ (}\%\text{)} & (t_{50})_{30}\text{ (}\%\text{)} & (t_{25})_{30}\text{ (}\%\text{)} & (t_{4})_{30}\text{ (}\%\text{)} & (t_{2})_{30}\text{ (}\%\text{)}\\ | ||
(t_{75})_{50}\text{ (}\%\text{)} & (t_{50})_{50}\text{ (}\%\text{)} & (t_{25})_{50}\text{ (}\%\text{)} & (t_{4})_{50}\text{ (}\%\text{)} & (t_{2})_{50}\text{ (}\%\text{)}\\ | |||
\end{bmatrix}_{\rm Bed,m}\\ | \end{bmatrix}_{\rm Bed,m}\\ | ||
\end{bmatrix},\;\;\;\;\;\; | \end{bmatrix},\;\;\;\;\;\; | ||
Line 112: | Line 220: | ||
\begin{bmatrix} | \begin{bmatrix} | ||
(d_{\rm p})_1\text{ (mm)} & \dots & (d_{\rm p})_k\text{ (mm)} \\ | (d_{\rm p})_1\text{ (mm)} & \dots & (d_{\rm p})_k\text{ (mm)} \\ | ||
\end{bmatrix}\\ | \end{bmatrix}_{\rm Bed}\\ | ||
\begin{bmatrix} | \begin{bmatrix} | ||
( | (E_{\rm cs})_{10,1}\text{ (kWh/t)} & \dots & (E_{\rm cs})_{10,k}\text{ (kWh/t)}\\ | ||
( | (E_{\rm cs})_{30,1}\text{ (kWh/t)} & \dots & (E_{\rm cs})_{30,k}\text{ (kWh/t)}\\ | ||
( | (E_{\rm cs})_{50,1}\text{ (kWh/t)} & \dots & (E_{\rm cs})_{50,k}\text{ (kWh/t)}\\ | ||
\end{bmatrix}_{\rm Bed,1}\\ | \end{bmatrix}_{\rm Bed,1}\\ | ||
\vdots\\ | \vdots\\ | ||
\begin{bmatrix} | \begin{bmatrix} | ||
( | (E_{\rm cs})_{10,1}\text{ (kWh/t)} & \dots & (E_{\rm cs})_{10,k}\text{ (kWh/t)}\\ | ||
( | (E_{\rm cs})_{30,1}\text{ (kWh/t)} & \dots & (E_{\rm cs})_{30,k}\text{ (kWh/t)}\\ | ||
( | (E_{\rm cs})_{50,1}\text{ (kWh/t)} & \dots & (E_{\rm cs})_{50,k}\text{ (kWh/t)}\\ | ||
\end{bmatrix}_{\rm Bed,m}\\ | \end{bmatrix}_{\rm Bed,m}\\ | ||
\end{bmatrix} | \end{bmatrix} | ||
Line 128: | Line 237: | ||
where: | where: | ||
* <math>n</math> is the number of size intervals | * <math>n</math> is the number of size intervals | ||
* <math>m</math> is the number of ore types | * <math>m</math> is the number of ore types | ||
Line 146: | Line 242: | ||
* <math>d_{i+1}<d_i<d_{i-1}</math>, i.e. descending size order from top size (<math>d_{1}</math>) to sub mesh (<math>d_{n}=0</math> mm) | * <math>d_{i+1}<d_i<d_{i-1}</math>, i.e. descending size order from top size (<math>d_{1}</math>) to sub mesh (<math>d_{n}=0</math> mm) | ||
* <math>Q_{\rm M,F}</math> is the mass flow rate of particles in the crusher feed (t/h) | * <math>Q_{\rm M,F}</math> is the mass flow rate of particles in the crusher feed (t/h) | ||
* <math>(t_{y})_x</math> is the fraction of mass passing one-<math>y</math>th the size of a parent particle (%) when <math>x\%</math> passes one-tenth the size of a parent particle (%), <math>y\in\{75, 50, 25,2\}</math>, <math>x\in\{10, 20, 30\}</math> | * <math>(t_{y})_x</math> is the fraction of mass passing one-<math>y</math>th the size of a parent particle (%) when <math>x\%</math> passes one-tenth the size of a parent particle (%), <math>y\in\{75, 50, 25, 2\}</math>, and <math>x\in\{10, 20, 30\}</math> or <math>x\in\{10, 30, 50\}</math> | ||
* <math>d_{\rm p}</math> is the size of a parent particle subject to breakage for Energy-Size Reduction relationship testing (mm) | * <math>d_{\rm p}</math> is the size of a parent particle subject to breakage for Energy-Size Reduction relationship testing (mm) | ||
* <math>k</math> is the number of particle sizes subject to breakage for Energy-Size Reduction relationship testing | * <math>k</math> is the number of particle sizes subject to breakage for Energy-Size Reduction relationship testing | ||
* <math>( | * <math>(E_{\rm cs})_{x,k}</math> is the specific comminution energy required to break a parent particle of size <math>(d_p)_k</math> into a distribution of progeny particles with <math>x\%</math> passing one-tenth of the parent size (kWh/t) | ||
* the <math>\rm SP</math> subscript indicates properties associated with ''single particle'' breakage | * the <math>\rm SP</math> subscript indicates properties associated with ''single particle'' breakage | ||
* the <math>\rm Bed</math> subscript indicates properties associated with ''bed compression'' breakage | * the <math>\rm Bed</math> subscript indicates properties associated with ''bed compression'' breakage | ||
Line 164: | Line 260: | ||
x_{\rm c}\text{ (m)}\\ | x_{\rm c}\text{ (m)}\\ | ||
f\text{ (frac)}\\ | f\text{ (frac)}\\ | ||
c\text{ (frac)}\\ | |||
Q\text{ (t/h)}\\ | Q\text{ (t/h)}\\ | ||
P_{\rm Pre}\text{ (kW)}\\ | P_{\rm Pre}\text{ (kW)}\\ | ||
Line 227: | Line 323: | ||
where: | where: | ||
* <math>Q_{\rm M,P}</math> is the mass flow rate of particles in the overall, combined product (t/h) | * <math>Q_{\rm M,P}</math> is the mass flow rate of particles in the overall, combined product (t/h) | ||
* <math>Q_{\rm M,E}</math> is the mass flow rate of particles in the ''edge'' product (t/h) | * <math>Q_{\rm M,E}</math> is the mass flow rate of particles in the ''edge'' product (t/h) | ||
Line 325: | Line 416: | ||
|- | |- | ||
|K1 | |K1 | ||
|style="background: #eaecf0" | Display | |style="background: #eaecf0" | Input / Display | ||
|K1 parameter for Pre, Bed and Edge crushers. | |K1 parameter for Pre, Bed and Edge crushers. | ||
|- | |- | ||
Line 370: | Line 461: | ||
{{SysCAD (Page, About)}} | {{SysCAD (Page, About)}} | ||
==== Additional notes ==== | |||
{{SysCAD (Text, HPGR, No PSD Splits)}} | |||
== See also == | |||
* [[HPGR (Torres)|Torres HPGR model]] | |||
* [[HPGR (Campos)|Campos HPGR model]] | |||
* [[Crusher (Whiten)|Whiten crusher model]] | |||
== References == | == References == |
Latest revision as of 11:55, 18 June 2023
Description
This article describes the Morrell-Tondo-Shi (Morrell et al., 1997) model for comminution by High Pressure Grinding Rolls (HPGR), verified for simulation and scale-up by Daniel and Morrell (2004).[1][2]
Model theory
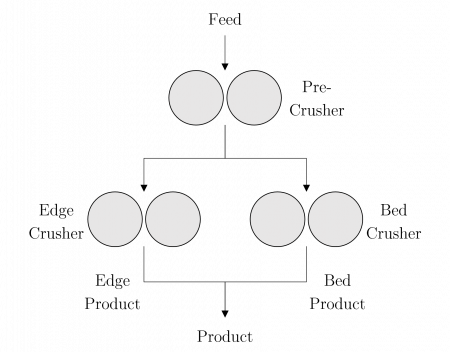
The Morrell-Tondo-Shi (Morrell et al., 1997) model simulates HPGR size reduction by linking three separate instances of the Whiten crusher model.[1] The crusher instances represent comminution by the sub-processes of pre-crushing, edge crushing, and compressed bed crushing, as illustrated in Figure 1.
Pre, edge and bed crushers
- Main article: See Crusher (Whiten) for a full description of the Whiten crusher model.
Behaviour of the pre-crusher process is determined by the critical gap, (mm), which is defined as the largest particle in the feed which will be nipped and comminuted in the HPGR machine. The critical gap can be estimated by the relation:
where:
- is the diameter of the rolls (m)
- is the working gap (m)
- is the bulk density of the discharge cake solids (t/m3)
- is the bulk density of the feed solids (t/m3)
The pre, edge and bed Whiten crusher parameter values in Table 1 are recommended by Morrell et al. (1997):
Whiten crusher parameter values for the Morrell-Tondo-Shi HPGR model (after Morrell et al., 1997).[1] Pre-crusher Edge crusher Bed crusher
Particles in the pre-crusher and edge crusher zones are assumed to undergo a single-particle breakage process, much like a conventional cone crusher:
- The appearance function and energy-size reduction parameters determined from drop weight tests characterise single particle breakage behaviour.
Particles in the bed crusher are subject to contact forces from surrounding particles and undergo a compressed bed breakage process:
- Compressed bed appearance function and energy-size reduction parameters may be determined from piston and die tests, and are notably different from the single particle breakage parameters for the same ore.
- The appearance function and energy-size reduction matrices for compressed bed breakage are specified at intervals, rather than the intervals of single particle breakage, due to the additional size reduction obtained from HPGR devices.
Edge split
The split of pre-crushed material to the edge crusher process, (frac), is given by:
where:
- is the edge split factor (-)
- is the length of the rolls (m)
Throughput
The throughput capacity of an HPGR machine may be estimated from:[2]
where
- is the HPGR throughput solids mass flow rate (t/h)
- is the circumferential velocity of the rolls (m/s)
- is the length of the rolls (m)
- is the working gap (m)
- is the discharge cake solids bulk density (t/m3)
The parameter is a correction factor applied to the theoretical throughput to account for material slip at the rolls face:
where is the measured throughput of an HPGR unit (t/h) and is the theoretical throughput calculated from (t/h).
Morrell et al. (1997) suggests material slip is a function of rolls speed and the dimensionless rolls gap, and that the correction factor exhibits a linear relationship of the form , i.e.:
The parameters and can be determined from measurements on an operating HPGR at various throughputs, roll speeds and working gaps.
Power
The gross power draw of the HPGR machine, (kW), is computed as:
where:
- is the no-load (idling) power draw of the machine (kW)
- is the power draw estimated by the pre-crusher model (kW)
- is the power draw estimated by the edge crusher model (kW)
- is the power draw estimated by the compressed bed crusher model (kW)
- and are user-defined scaling factors that correct model-estimated power to observed power (kW/kW)
The specific comminution energy, (kWh/t), of an HPGR is defined as:
Excel
The Morrell-Tondo-Shi HPGR model may be invoked from the Excel formula bar with the following function call:
=mdUnit_HPGR_MorrellTondoShi(Parameters as Range, Size as Range, HPGRFeed as Range, SP_Appearance as Range, SP_Ecst10Size-t10-size as Range, Bed_Appearance as Range, Bed_Ecst10Size as Range)
Invoking the function with no arguments will print Help text associated with the model, including a link to this page.
Inputs
The required inputs are defined below in matrix notation with elements corresponding to cells in Excel row () x column () format:
where:
- is the number of size intervals
- is the number of ore types
- is the size of the square mesh interval that mass is retained on (mm)
- , i.e. descending size order from top size () to sub mesh ( mm)
- is the mass flow rate of particles in the crusher feed (t/h)
- is the fraction of mass passing one-th the size of a parent particle (%) when passes one-tenth the size of a parent particle (%), , and or
- is the size of a parent particle subject to breakage for Energy-Size Reduction relationship testing (mm)
- is the number of particle sizes subject to breakage for Energy-Size Reduction relationship testing
- is the specific comminution energy required to break a parent particle of size into a distribution of progeny particles with passing one-tenth of the parent size (kWh/t)
- the subscript indicates properties associated with single particle breakage
- the subscript indicates properties associated with bed compression breakage
Results
The results are displayed in Excel as an array corresponding to the matrix notation below:
where:
- is the mass flow rate of particles in the overall, combined product (t/h)
- is the mass flow rate of particles in the edge product (t/h)
- is the mass flow rate of particles in the bed (centre) product (t/h)
Example
The images below show the selection of input arrays and output results in the Excel interface.
SysCAD
The sections and variable names used in the SysCAD interface are described in detail in the following tables.
MD_HPGR page
The first tab page in the access window will have this name.
Tag (Long/Short) | Input / Display | Description/Calculated Variables/Options |
---|---|---|
Tag | Display | This name tag may be modified with the change tag option. |
Condition | Display | OK if no errors/warnings, otherwise lists errors/warnings. |
ConditionCount | Display | The current number of errors/warnings. If condition is OK, returns 0. |
GeneralDescription / GenDesc | Display | This is an automatically generated description for the unit. If the user has entered text in the 'EqpDesc' field on the Info tab (see below), this will be displayed here.
If this field is blank, then SysCAD will display the unit class ID. |
Requirements | ||
On | CheckBox | This enables the unit. If this box is not checked, then the material will pass straight through the crusher with no change to the size distribution. |
Method | Fixed Discharge | The discharge particle size distribution is user defined. Different distributions can be used for different solids. |
Morrell-Shi-Tondo | The throughput, power draw and product size distribution are determined by the Morrell-Tondo-Shi model. Different parameters can be used for different solids. | |
Torres | The throughput, power draw and product size distribution are determined by the Torres model. Different parameters can be used for different solids. | |
Campos | The throughput, power draw and product size distribution are determined by the Campos model. Different parameters can be used for different solids. | |
Options | ||
ShowQFeed | CheckBox | QFeed and associated tab pages (eg Sp) will become visible, showing the properties of the combined feed stream. |
ShowQProd | CheckBox | QProd and associated tab pages (eg Sp) will become visible, showing the properties of the products. |
SizeForPassingFracCalc | Input | Size fraction for % Passing calculation. The size fraction input here will be shown in the Stream Summary section. |
FracForPassingSizeCalc | Input | Fraction passing for Size calculation. The fraction input here will be shown in the Stream Summary section. |
Stream Summary | ||
MassFlow / Qm | Display | The total mass flow in each stream. |
SolidMassFlow / SQm | Display | The Solids mass flow in each stream. |
LiquidMassFlow / LQm | Display | The Liquid mass flow in each stream. |
VolFlow / Qv | Display | The total Volume flow in each stream. |
Temperature / T | Display | The Temperature of each stream. |
Density / Rho | Display | The Density of each stream. |
SolidFrac / Sf | Display | The Solid Fraction in each stream. |
LiquidFrac / Lf | Display | The Liquid Fraction in each stream. |
Passing | Display | The mass fraction passing the user-specified size (in the field SizeForPassingFracCalc) in each stream. |
Passes | Display | The user-specified (in the field FracForPassesSizeCalc) fraction of material in each stream will pass this size fraction. |
HPGR page
The HPGR page is used to specify the input parameters for the HPGR model.
Ore page
This page is used to define the crusher comminution properties of SysCAD species with the size distribution quality in the project.
About page
This page is provides product and licensing information about the Met Dynamics Models SysCAD Add-On.
Tag (Long/Short) | Input / Display | Description/Calculated Variables/Options |
---|---|---|
About | ||
HelpLink | ![]() |
Opens a link to the Installation and Licensing page using the system default web browser. Note: Internet access is required. |
Information | ![]() |
Copies Product and License information to the Windows clipboard. |
Product | ||
Name | Display | Met Dynamics software product name |
Version | Display | Met Dynamics software product version number. |
BuildDate | Display | Build date and time of the Met Dynamics Models SysCAD Add-On. |
License | ||
File | ![]() |
This is used to locate a Met Dynamics software license file. |
Location | Display | Type of Met Dynamics software license or file name and path of license file. |
SiteCode | Display | Unique machine identifier for license authorisation. |
ReqdAuth | Display | Authorisation level required, MD-SysCAD Full or MD-SysCAD Runtime. |
Status | Display | License status, LICENSE_OK indicates a valid license, other messages report licensing errors. |
IssuedTo | Display | Only visible if Met Dynamics license file is used. Name of organisation/seat the license is authorised to. |
ExpiryDate | Display | Only visible if Met Dynamics license file is used. License expiry date. |
DaysLeft | Display | Only visible if Met Dynamics license file is used. Days left before the license expires. |
Additional notes
When the edge stream is connected, the following applies to mass splits:
- Solid species without a particle size distribution property are split to the edge stream according to the overall mass split of the default particle size distribution species selected in the SysCAD Project Configuration
- If the default particle size distribution species is not present in the unit feed, the overall split of all other species with particle size distributions combined is used, as determined by the model.
- Liquids species are split between the edge and product streams in the same proportion as solid species.
- Gas phase species report directly to the product stream without split.
See also
References
- ↑ 1.0 1.1 1.2 1.3 Morrell, S., Tondo, L.A., and Shi, F., 1997. Modelling and scale-up of high pressure grinding rolls. In Proc. XX International Mineral Processing Congress, Aachen, Germany, September 1997.
- ↑ 2.0 2.1 Daniel, M.J. and Morrell, S., 2004. HPGR model verification and scale-up. Minerals Engineering, 17(11-12), pp.1149-1161.